Aerospace Industry
The aerospace industry designs and builds aircraft, spacecraft, and related systems. It plays a big role in improving transportation, defense, and space exploration, creating new technologies that help connect the world and explore space.
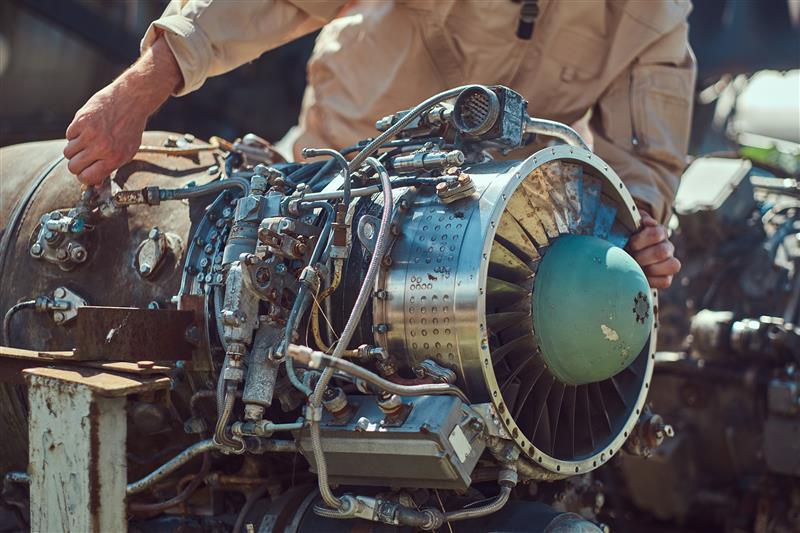
Initial Challenge or Current Challenges
Aircraft maintenance checks are essential because they can help detect problems early, lowering the risk of accidents. The aerospace industry faces numerous challenges with traditional visual inspection and quality control. Relying on manual inspection can lead to mistakes with repetitive tasks, where attention to detail may decline. This raises safety concerns, as even small flaws can impact the performance of aerospace components. Manual inspections are time-consuming and labor-intensive, which can delay production timelines, lead to costly recalls, and affect delivery schedules. In aerospace maintenance, Surface-level defects are flaws on the exterior of parts, often caused by manufacturing errors. Common surface issues include scratches and abrasions from handling or tooling, which can weaken the material; cracks from stress or improper heat treatment, which may grow under pressure corrosion from moisture or chemical exposure that degrades metal parts over time. Pitting weakens structural integrity and may lead to cracks and discoloration, signaling possible material degradation or overheating. On the other hand, internal defects are hidden within the material, including voids and inclusions that weaken the material which can cause fractures under stress. In composites, delamination occurs when layers separate, reducing the part’s strength. Porosity, or tiny holes in materials weakens the structure in cast or welded parts. Internal cracks can grow under pressure, leading to failure and inadequate bonding in layered or welded components that can cause parts to detach.
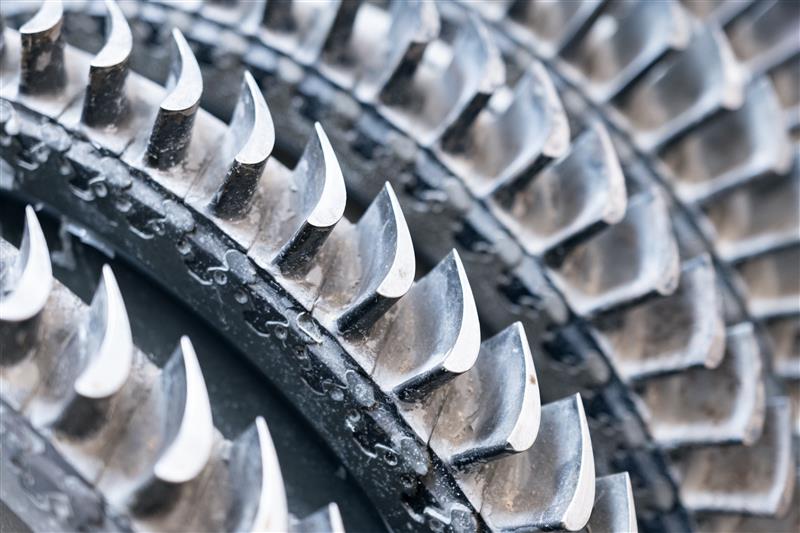
Implementation By xis.ai
xis.ai Suite provides powerful software infrastructure that can tackle these challenges by AI-powered systems. AI-powered quality inspection can detect surface-level and internal defects, addressing challenges faced by traditional methods. AI can analyze high-resolution images from cameras that can identify surface defects like scratches, cracks, and corrosion and can quickly spot even tiny changes or irregularities on the surface that may signal damage. AI identifies defects consistently across all parts, This can lead to more reliable detection of scratches, pitting, and discoloration which maintain quality standards. Real-time monitoring can instantly flag defects as they appear on the production line. Internal defects can be detected with X-ray-based Non-Destructive Testing (NDT) that can detect internal flaws such as voids, inclusions, and cracks to spot tiny hidden defects that would be difficult for the human eye to detect. Deep learning models analyze internal structures, finding voids, delamination, or bonding issues in complex, layered, or welded parts where internal defects are hard to detect manually. AI systems gather and analyze data on defect patterns, allowing manufacturers to refine processes and make adjustments to reduce future defects.
Benefits
xis.ai for quality inspection offers numerous benefits. The automation of inspections speeds up the quality-check process, allowing for real-time monitoring and quicker identification of issues, which leads to reduced production delays and faster time-to-market. xis.ai provides a standardized approach, maintaining consistent quality control in all products while minimizing variability and saving costs by avoiding expensive recalls.