Deep Learning and AI: Redefining Industrial Inspection
Recent Post:
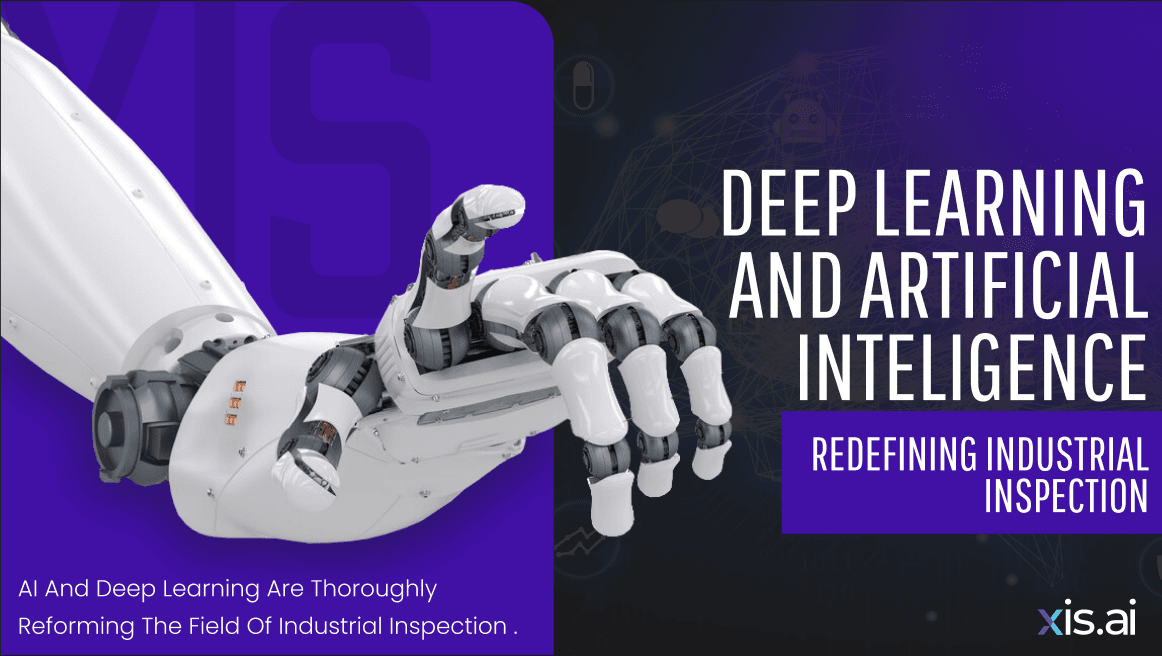
Artificial Intelligence (AI) and Deep learning (DL) are causing an outbreak in industrial inspection by using neural networks that can learn from small and big data sets. These systems are good at finding defects even in tricky or dynamic environments where regular software often can't cope. AI models are trained to spot acceptable product differences, and they can deal with all sorts of manufacturing situations without needing constant manual adjustments. In robotics, AI improves autonomous navigation, object handling, and predicting maintenance, which increases the productivity and safety of robotic systems across different industries.
These breakthroughs allow for on-the-spot inspection, quicker choices, and less downtime on production lines.
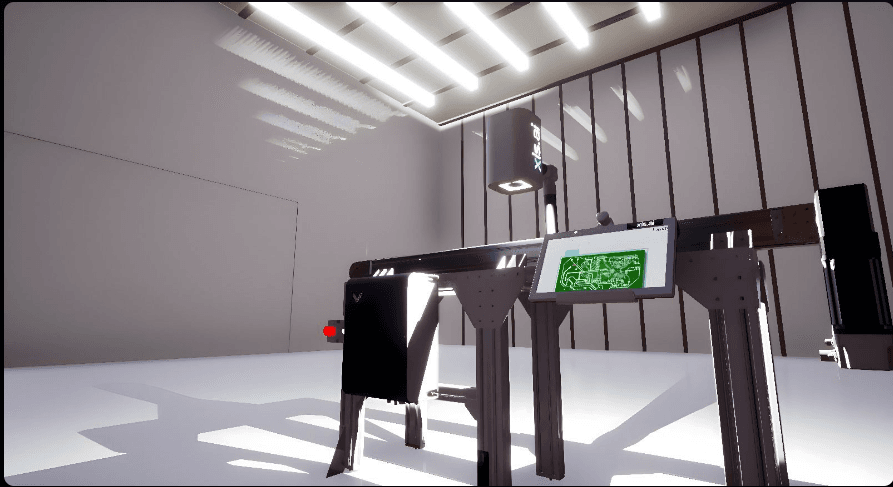
Improving Industrial Inspections with AI
Traditional industrial inspections, reliant on manual oversight and rule-based systems, work well for simple parts but struggle with complex, variable environments. People make mistakes when they check things by hand, and regular computer programs aren't flexible enough to spot tricky flaws that means they're not correct and cost more as you try to do.
Deep learning, which is part of AI, offers a better way. It uses neural networks to sort pictures. Training such models used to require larger datasets but recent advancements now enable training with fewer or no defective samples, making it more practical for manufacturers. AI also handles variability in organic products like meat or wood, improving precision and profitability.
By parallel processing and user-friendly tools this transformation is driven, allowing manufacturers to integrate AI-driven inspections for smarter, scalable solutions.
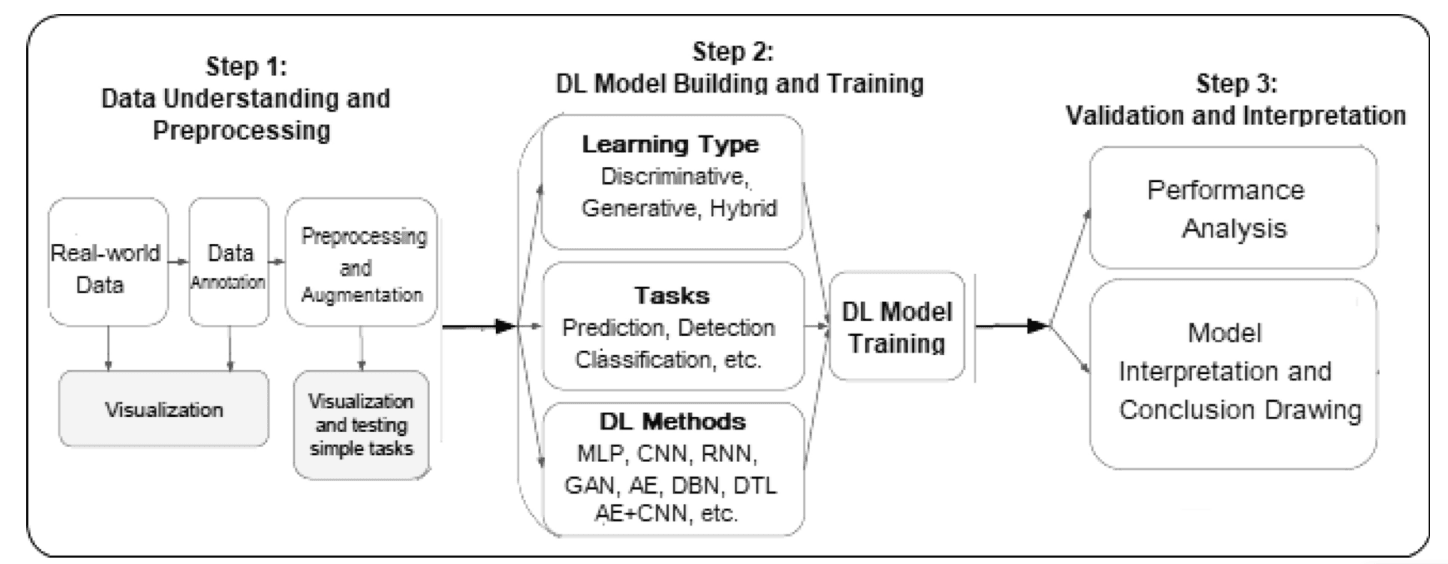
A typical DL workflow to solve real-world problems, which consists of three sequential stages (i) data understanding and preprocessing (ii) DL model building and training (iii) validation and interpretation Source
Why is AI Important in Industrial Inspection?
a) Computer Vision and Image Processing
Computer Vision (CV) is the basis of AI-based inspection systems which engages in processing and analyzing images or video visuals to inspect quality, detect defects and classify objects. The algorithms of CV utilize data of images captured from industrial cameras to examine the probity of products on the production line.
Convolutional Neural Network (CNNs) have an important role in enabling these systems. CNNs are skilled at observing patterns in image data, learning graded features like textures, edges and complex shapes. These models have become the support of AI-based inspection due to their ability to handle high-dimensional image data smoothly.
How CNNs Work in Industrial Inspection:
Preprocessing: Images that are preprocessed to optimize lighting conditions, removing noise, improving the clarity of defect regions are captured by production lines.
Feature Extraction: Layers of CNNs obtains low to high-level features such as edges, textures, and more complex structures, allowing the model to detect subtle differences between defective and non-defective products.
Classification: Images based on predefined classes are classified by models. (e.g., pass or fail, different types of defects).
Post Processing: Results are passed through decision layers to determine the necessary action, such as flagging the defective product or triggering further analysis.
b) Anomaly Detection Using Deep Learning
AI surpasses due to the predictable nature and repetition of tasks in industrial quality inspection, which makes it ideal for training neural networks for classification, object detection, or anomaly detection.
The basic technique in this area is anomaly detection, where a network is trained using only "good" examples. The network learns what is normal, flagging anything outside this dataset as abnormal, or an anomaly.
When "good" data is plotted, it forms a blob where anything within is normal, and anything outside is anomalous. This method is useful when few or no defective samples are available, common in industries where defects are rare or poorly documented.
For this specification, Autoencoders and Variational Autoencoders (VAEs) are widely utilized. Anomalies are detected by recognizing abnormalities from patterns that are expected by compressed representations of defect-free figures.
Steps in Anomaly Detection with Autoencoders:
1. Encoder: Into Latent representation the input image is compressed.
2. Decoder: From the compressed data the image is reconstructed.
3. Loss Calculation: Measures the reconstruction error between the original and reconstructed images. A high error suggests an anomaly.
This approach enables effective defect detection without extensive labeled data, improving the efficiency and accuracy of industrial quality inspection.
c) Object Detection and Segmentation for Defect Localization
When products are classified simply as defective or non-defective, industrial applications sometimes require defect localization to identify where defects occur. Object detection and semantic segmentation techniques are particularly useful in this regard.
Object Detection: Techniques like YOLO (You Only Look Once) and Faster R-CNN are used to detect specific defects by drawing bounding boxes around regions of interest in an image. This aids in locating large defects like surface scratches or structural damage.
Semantic Segmentation: More granular defects (such as microcracks or minute surface imperfections) require pixel-level precision. Semantic segmentation networks like UNet or Mask R-CNN segment images into defective and non-defective areas, enabling precise identification and localization of defects.
3. Data Requirements and Model Training
The deep learning models used in industrial inspection need large amounts of labeled data for effective training. This includes both images of defect-free and defective products. However, generating defect data can be challenging, especially for industries where defects are rare.
Data Augmentation Techniques: To address the scarcity of defect data, AI engineers employ techniques like:
Rotation and Scaling: Augmenting the dataset by rotating or scaling images to simulate different viewpoints or sizes of defects.
Noise Addition: Adding Gaussian noise or adjusting lighting conditions can improve the model’s durability to real-world variations.
Transfer Learning: Transfer learning is commonly used in industrial inspection, where models pre-trained on large datasets like ImageNet are fine-tuned on specific industrial datasets. This reduces training time and reduces the problem of limited data in niche industries.
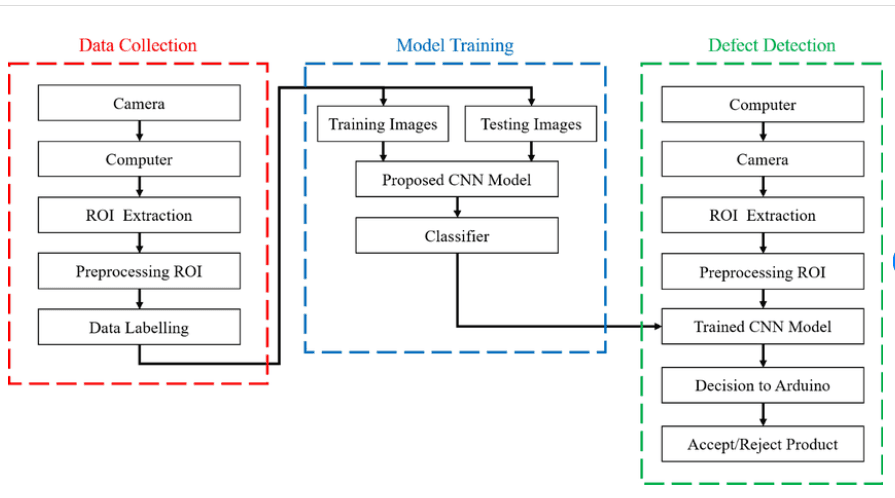
Steps of proposed deep learning-based industrial inspection system framework Source
Applications Across Industries
AI-based industrial inspection is being established in multiple sectors, each with innovative challenges and requirements:
a) Electronics Manufacturing
The circuit boards endure inspection for defects such as flaws, missing components, or misalignments in electronics manufacturing. Optical character recognition (OCR) systems also make sure that labels and serial numbers are correctly printed on products on which deep learning is based.
b) Pharmaceuticals
Using deep learning visual inspection of syringes and vials for damage is automated. Packaging, labeling, and sealing of medications meet regulatory standards in the pharmaceutical industry because of AI systems that detect packaging defects and missing labels, ensuring safety and compliance.
c) Automotive Industry
Automotive parts are checked by deep learning models for things like surface scratches, welding defects, and strength issues. Advanced images are utilized by these models for analysis to spot problems in engines, frames, and electronic parts, helping to make vehicles safer and more reliable.
Future Trends in AI-Based Industrial Inspection:
The future of AI-based inspection is bright, with several trends ready to improve even more.
Self-Learning Systems: Systems capable of continuously learning from new data and improving without human intervention will drive productivity.
Edge AI: With edge computing, AI models can be deployed directly on industrial devices, reducing latency and enabling real-time decision-making.
Integration with IoT: AI-based inspection will integrate with IoT devices for more durable data collection and analysis, facilitating end-to-end monitoring and predictive maintenance.
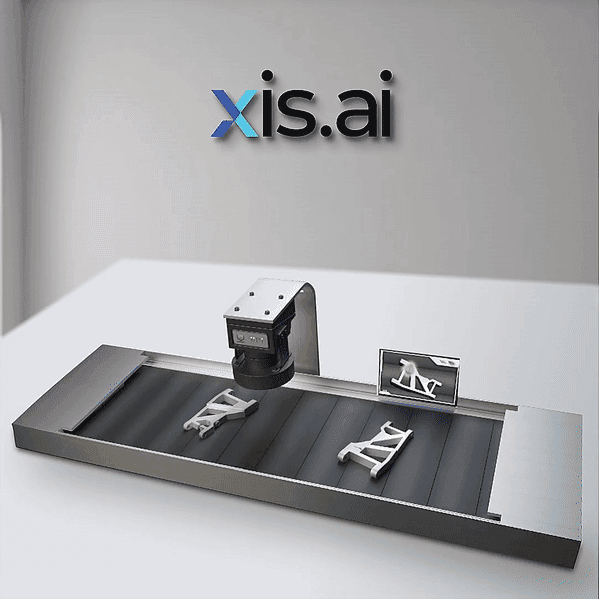
Conclusion:
AI and deep learning are thoroughly reforming the field of industrial inspection accurately, delivering faster and more scalable solutions. From computer vision systems detecting surface defects to anomaly detection models flagging unseen faults. Data and computational capabilities continue to grow, we can expect even more sophisticated AI-based inspection systems that push the boundaries of what is possible in modern manufacturing. AI is enabling industries to meet higher quality standards while reducing costs and inefficiencies.
About xis.ai
xis.ai automates visual quality inspection with AI and robotics. With a camera and no code computer vision platform that enables non-technical industrial users to develop, deploy, and use Automated Visual Inspection (AVI) in any industry in minutes.
Comment
0Comments
No comments yet.